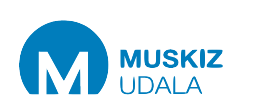

Capítulo X
Los hornos de calcinar carbonatos
Por debajo de las enormes veneras de los Montes de Triano se encontraban grandes masas de carbonato de hierro que había sido despreciado por contener una mena muy inferior a la de los óxidos. Sin embargo, a finales del siglo XIX el agotamiento del rico mineral despertó el ingenio de geólogos e ingenieros de minas. En teoría, la solución para el aprovechamiento de los carbonatos pasaba por la calcinación. De ese modo, al calcinarlos se eliminarían impurezas como el azufre y el sílice; se aumentaría la mena; y se conseguiría reducir la masa mineral abaratando el transporte, así como un producto de mayor calidad propicio para su utilización en los altos hornos.
No obstante, se pensaba que la reducción daría un material polvoriento y de difícil aprovechamiento en los hornos altos, así que en 1882 el audaz e ingenioso José McLennan construyó un horno para experimentar y demostrar que los carbonatos calcinados podían perder parte de su dureza inicial y romperse fácilmente, aunque no con las manos. Fue así como consiguió trozos de mineral —no polvo— aptos para la producción de arrabio en las siderurgias.
Los hornos de calcinar fueron la solución que permitió el aprovechamiento de los carbonatos al eliminar impurezas y aumentar su ley en un veinte por ciento. El carbonato cálcico era un mineral grisáceo y, al calcinarse y enfriarse, se volvía de un color rojizo similar a la vena.
En años sucesivos, el ingeniero escocés construyó tres hornos más en Amalia Vizcaína. Los dos últimos fueron de una gran capacidad (600 t) y, aunque se conservan en un lamentable estado, representan un importante patrimonio material que es necesario restaurar y proteger.
La construcción de hornos de calcinar supuso un nuevo impulso para la minería permitiendo la explotación de carbonatos, mineral que se utilizó hasta 1991. Los hornos fueron evolucionando con objeto de optimizar la calcinación, buscando calidad, cantidad y reducir el tiempo de cocción. Asimismo, variaron en tamaño y forma, mejoraron la inyección de aire para acelerar la combustión y los últimos incluso se construyeron íntegramente en hierro.
En Cobaron, la mina Josefa levantó seis hornos consiguiendo una gran producción de carbonato calcinado que transportaban hasta su cargadero de El Piquillo. Fueron de menor capacidad que los de Amalia Vizcaína y no se conservan restos.
Características de los hornos
Los hornos de calcinar de Amalia Vizcaína se construyeron aprovechando un fuerte talud en el terreno. En la parte superior del desnivel se acumulaban los materiales a utilizar en la carga, vagonetas en espera con carbonato de diferentes granulometrías o con carbón y las diversas herramientas que se utilizaban. Las bocas de cargue de los hornos estaban a la altura de esta zona de servicios, distanciadas por una decena de metros y unidas por una fuerte pasarela metálica.
Los hornos tenían una forma troncocónica. Su altura era de aproximadamente quince metros y la base exterior de otros ocho de diámetro. Estaban construidos con bloques de mampostería de piedra caliza unida con un mortero de arena de dolomía. Contaban con tres anillos metálicos exteriores denominados zunchos para evitar la dilatación por el calor de la combustión y la aparición de abombamientos o resquebrajamientos. Se levantaban sobre una robusta cimentación de piedra caliza. Los primeros dos metros de altura eran de un espesor considerable y contaban con un perímetro octogonal. Además, en cuatro de sus lados estaban las puertas de descarga, denominadas boquillas.
Las bocas de entrada de los hornos tenían una amplia pasarela circular dotada de una valla protectora sobre la que trabajaban los horneros con sus largas barras. Las vagonetas con el mineral pasaban por la pasarela metálica que unía el horno con la zona de servicios y rodeaban a este volcando mineral en los lugares indicados por los horneros, que siempre procuraban conseguir capas horizontales.
La sección interior de los hornos también era troncocónica y estaba recubierta con ladrillo refractario fijado con morteros de arena de dolomía. Los dos hornos que se conservan no se construyeron al mismo tiempo: el más antiguo contó con un revestimiento interior hecho en base a tortas de mortero de dolomía que se adherían a la caliza, pero las fuertes combustiones las disgregaban con facilidad y las reparaciones eran muy habituales, así que al construir el segundo horno se modificó el primero revistiéndolo de ladrillos refractarios.
La base de los hornos se denominaba solera, plaza o crisol. Era un cono de hierro fundido que ocupaba todo el interior circular, con las caídas hacia las boquillas para facilitar la salida del carbonato calcinado.
Entre el ladrillo fábrica y la solera había unas toberas que permitían que entrara el aire necesario para la combustión, que se aceleraba o ralentizaba abriendo las puertas de las boquillas.
Las descargas de mineral calcinado eran diarias y se hacían de forma coordinada por las cuatro boquillas. El mineral era arrastrado hasta unas vertederas con base de traviesas y chapas donde estaban las tolvas. Debajo entraban los vagones del tren para ser cargados. Los materiales se transportaban según necesidad, dependía del acopio en la vertedera de los hornos o del acopio en el cargadero de El Castillo. La máquina no funcionaba todos los días, sino que tan solo cuando había necesidad hacía varios viajes al día. En los últimos años, la vía era ya vieja y de costoso mantenimiento, por lo que el transporte se realizó con camiones. Todo el mineral que se embarcaba para el extranjero iba calcinado.
Los ladrillos refractarios del interior de los hornos se disgregaban por el calor y era necesario un mantenimiento regular que consistía en cambiarlos o cubrirlos con mortero de arenas de dolomía. En este caso los operarios trabajaban en el interior, con temperaturas muy elevadas y sobre andamios de madera.
Estas reparaciones se hacían con el horno caliente, no se dejaba enfriar del todo, así que el mantenimiento era arduo y peligroso.
Era difícil arrancar el horno, prenderlo y volver a conseguir una combustión homogénea, por lo que se procuraba emplear madera de borto que se traía de los montes cercanos o árgomas que se habían plantado en las zonas de las antiguas escombreras.
Funcionamiento de los hornos
De la zona de selección de mineral partían unas pasarelas con raíles por las que los trabajadores empujaban las vagonetas hasta la boca del horno. Eran de pequeñas dimensiones, volcaban por ambos lados para facilitar la maniobra y tenían capacidad para una tonelada de material que el hornero echaba en el interior del horno cuando la carga descendía. Durante la maniobra procuraba echar mucha piedra y poco menudo, y sobre cada tonelada de mineral espolvoreaba cerca de treinta kilogramos de carbón menudo de buena calidad (antracita).
Cada horno tenía una carga constante de seiscientas toneladas de carbonatos que tardaban de tres a cuatro días en bajar y cocer. Su contenido se dividía en una parte superior fría; en otra intermedia donde se realizaba la combustión a unos novecientos grados centígrados y se quemaban las impurezas (azufre, zinc, silicio...); y una inferior, ya calcinada y fría. La carga de carbón era importante para mantener la combustión, además se introducía aire por las boquillas de descarga para acelerarla, de lo contrario, se ralentizaba.
Una buena calcinación dependía de la pericia y experiencia del hornero. La carga tenía que bajar de forma estable, sin desnivelarse, para evitar las temidas chimeneas, es decir, agujeros de abajo hacia arriba por los que entraba aire aumentando la temperatura en la zona de combustión y consiguiendo unas pastas de mineral fundido que eran muy difíciles de sacar por las piqueras. Cuando se originaba una chimenea, el hornero echaba rápidamente mineral menudo para taparla y mandaba cerrar las puertas de las boquillas para evitar la entrada de aire y ralentizar la combustión.
Las chimeneas se originaban por diversos motivos, por ejemplo, por piedras de carbonatos más dúctiles que originaban huecos o también que se calentase el horno por una parte y por la otra se fuese enfriando, pero lo más importante era sacar el mineral calcinado por las cuatro boquillas a la vez para evitar la desestabilización de la zona intermedia. Estas temidas pastas ocasionaban muchos problemas taponando la salida del mineral calcinado y, aunque se rompían con porras y barras, en ocasiones eran necesarias pequeñas cargas de dinamita para fraccionarlas.
Los hornos no paraban nunca, siempre había carga cociéndose. A medida que el mineral se reducía y perdía tamaño, la carga bajaba, por lo que el hornero volcaba más mineral por la boca, mientras que por las boquillas sacaba el mineral calcinado a unas vagonetas que descargaban en las vertederas.
Los sábados y domingos no se extraía mineral calcinado, así que se les daba una marcha lenta para que no se apagasen. Los horneros trabajaban a dos turnos y, fuera del horario laboral o los fines de semana, siempre había un operario vigilando la combustión, la cual ralentizaba cerrando las boquillas para que entrase menos aire.
No se recuerdan accidentes.
